MEDIA CENTER
Mar 22th, 2024
High-frequency thermocompression welding on ZIP fabric blinds
The ZIP fabric blinds is a common type of roller shutter door and window system. It typically consists of fabric, guide rails, zippers, and other components, offering convenient opening and closing methods while also possessing excellent sealing and anti-theft capabilities. The application of high-frequency heat sealing welding on ZIP fabric blinds can enhance the durability and sealing of its connection parts. Here are some possible application methods:
Fabric Connection:
When manufacturing ZIP fabric blinds, it is often necessary to join the fabric with the zipper to ensure secure attachment.
High-frequency thermal compression welding can fuse the fabric with the zipper, creating a robust connection point, thus avoiding potential weaknesses associated with conventional sewing or adhesive bonding.
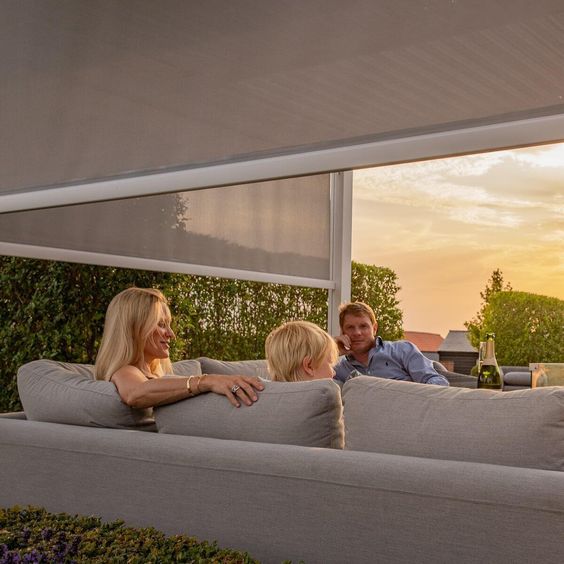
Edge Reinforcement:
ZIP fabric blinds typically require additional reinforcement along the edges to enhance durability and stability.
High-frequency thermal compression welding can reinforce tapes near the fabric edges, increasing durability and ensuring edge sealability to prevent dust and moisture infiltration.
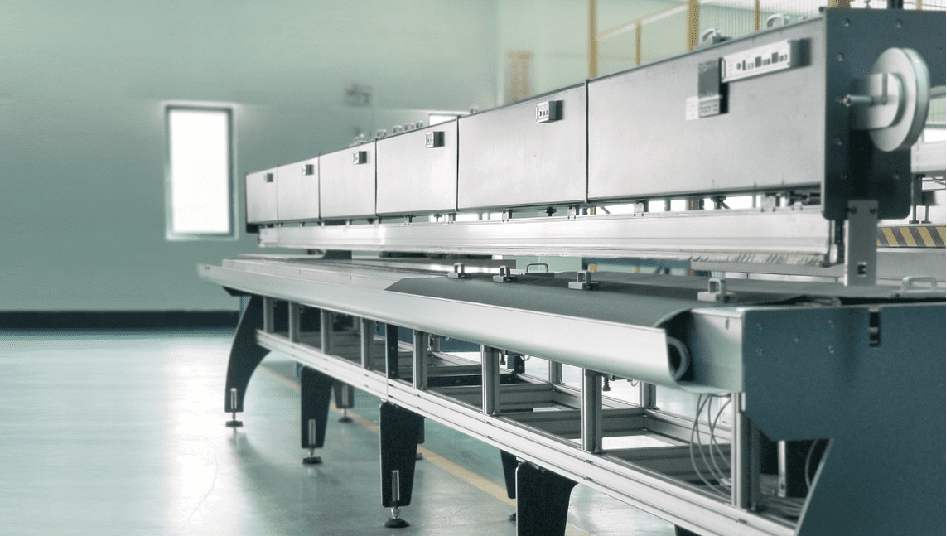
Sealing Treatment:
The sealing performance of ZIP fabric blinds is critical for controlling indoor temperature and humidity.
High-frequency thermal compression welding can create effective seals between the fabric and the guide rail, ensuring efficient insulation when the shutter is closed against external air, moisture, and dust.
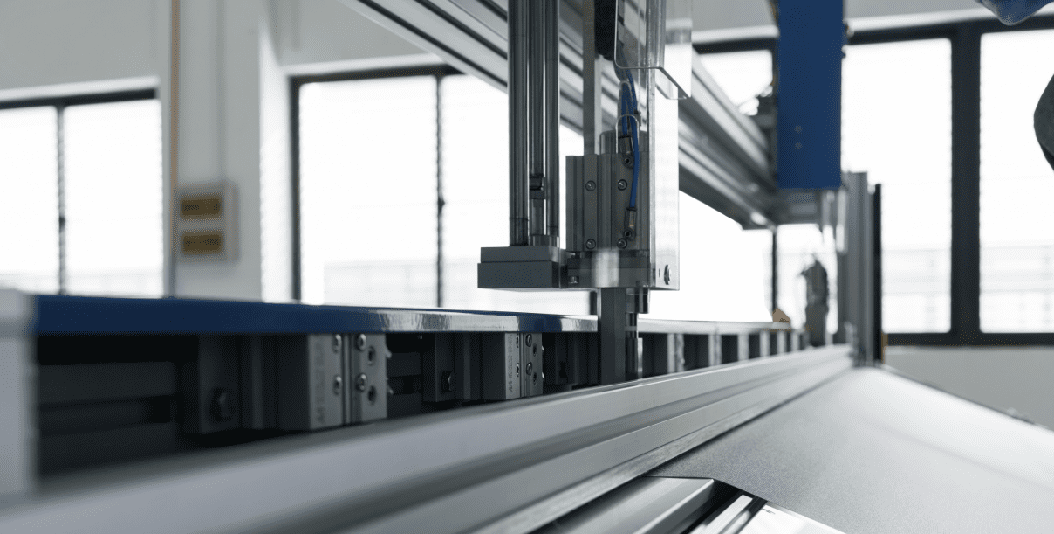
Aesthetic Enhancement:
High-frequency thermal compression welding enables seamless connections, resulting in a more aesthetically pleasing appearance of the roller shutter without visible welding marks or impurities, thereby enhancing overall product quality.
Improved Durability:
Utilizing high-frequency thermal compression welding for connections ensures higher strength and durability of the connection points, reducing maintenance and replacement costs due to joint loosening or damage.
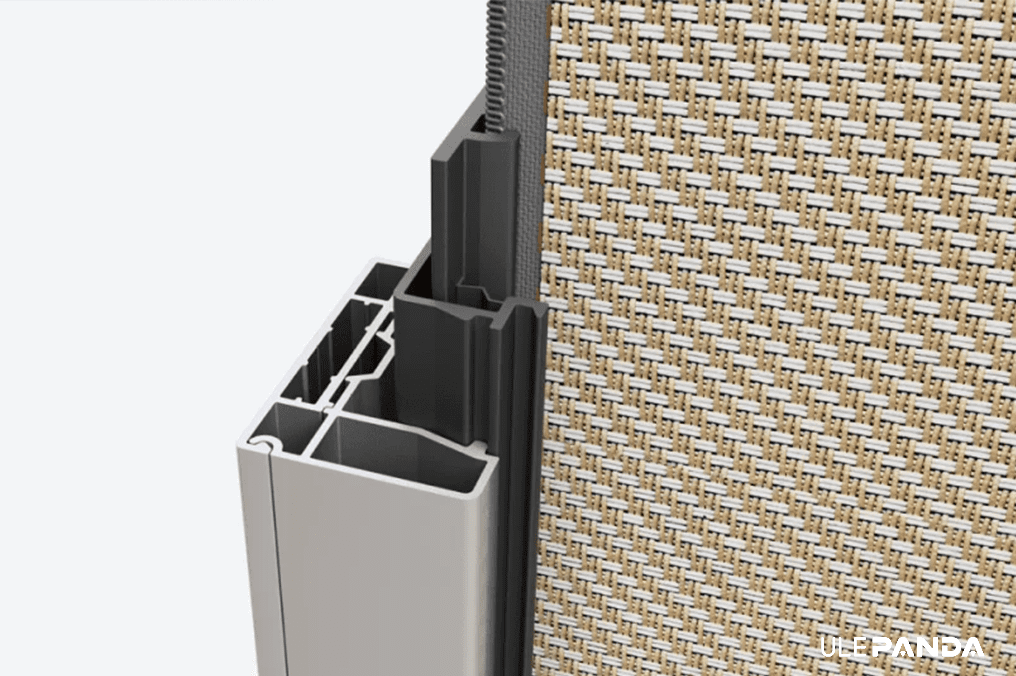
Brief introduction of High-frequency thermal compression welding
High-frequency thermal compression welding is a commonly used metal material joining process, also known as high-frequency induction thermal compression welding or high-frequency fusion overlay welding. It is mainly suitable for connecting metal pipes, wires, sheets, and other workpieces, commonly found in electronics, automotive, aerospace, and other fields. Below is a detailed introduction to this process:
Working Principle:
High-frequency thermal compression welding utilizes the principle of high-frequency induction heating. By applying a high-frequency electromagnetic field near the metal joint, it induces localized electric currents in the joint, thereby generating the heat required for welding.
Subsequently, when heated to a sufficient temperature, a certain pressure is applied to soften the metal material and reach the welding temperature, thus forming the weld.
Equipment Composition:
High-frequency thermal compression welding equipment typically consists of components such as high-frequency induction heating devices, pressure systems, and control systems.
The high-frequency induction heating device is used to generate a high-frequency electromagnetic field to locally heat the workpiece.
The pressure system is used to apply the required welding pressure.
The control system is used to control heating temperature, pressure, and other parameters during the welding process.
Advantages:
Fast: Utilizing high-frequency induction heating enables rapid heating, resulting in quick welding.
Uniform Temperature: High-frequency induction heating can precisely heat the workpiece locally, ensuring uniform distribution of welding temperatures.
High Welding Strength: Due to uniform heating, the weld quality is good, and the welding strength is usually high.
Contact us
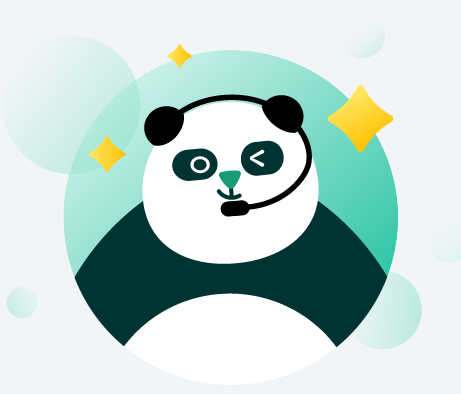
Kevin
Account Manager

info@ulepanda.com

+86 18913012012

+86 18913012012